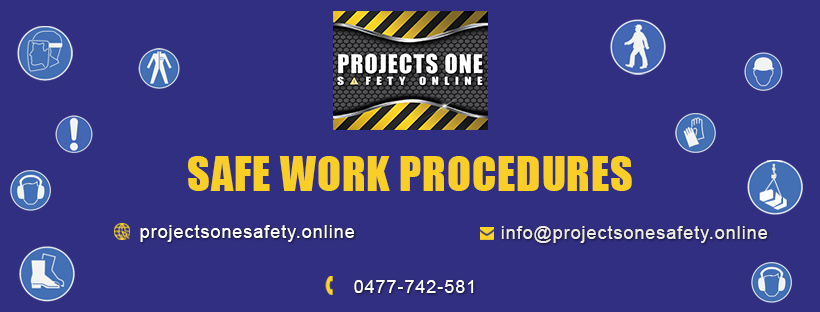
Safe Work Procedures
Writing Safe Work Procedures
If you read our last blog Back to Safety Basics you would have read about Safe Work Procedures (SWP). Now remember SWP have many names and acronyms such as Safe Work Instructions, Safe Work Practices, Safe Work Systems or Safe Operating Procedures. The way Projects One Safety Online has broken it down is that if you are operating plant, tools, equipment we call it a Safe Operating Procedure (SOP), if you are doing a task that has a number of hazards involved such as entering a confined space then we have Safe Work Procedures (SWP) for our teams to follow.
These documents allow us to use them when training new staff. It means everyone is trained the same way and allows us to monitor the procedure to ensure that it remains unchanged and in place. We can tell immediately if someone is trying to cut corners, this is when accidents happen.
Safe Work/Operating Procedures also give us a tool when doing a safety audit or if an incident or near miss should happen we have a standard to work from. We look at the current hazard control measures in place and look at how they can be improved. We also give the procedure to our team for checking over and to provide feedback as consultation with the team is a vital part of the process.
If writing an SOP or SWP baffles you beyond frustration keep reading.
10 tips to writing Safe Work Procedures
Written by, a Tradies Wife, creator of Projects One Safety Online, the ‘simplifier’ of all thing’s safety.
(I have used Worksafe Queensland as an example below as it is what I am most familiar with, each state follows similar rules and guidelines. Please check your own states website for further information. This is not a complete list and care should be taken to ensure you cover all aspects of your Safety)
“Some work tasks carry risks. Good risk management, including safe work procedures, ensure risk at your work is minimised and workers know how to perform tasks safely.”
Develop a SWP or an SOP for all tasks that could potentially harm your employees
- Look at each task and how it is broken down into smaller tasks e.g. Unloading mobile equipment from the back of a truck, 1. find flat stable ground 2. secure handbrake 3. secure wheel chocks…..
- Identify the hazards that could potentially harm your employees e.g. uncontrolled movement of truck or equipment, slipping while climbing onto truck..
- Consult your employees, they know the task best and it’s their safety you are determining
- Look for other sources of information that might help identify hazards such as codes of practice, operating manuals, manufacturer guidelines, safety data sheets
- Determine the level of risk – doing a risk assessment will help
- Now you know the hazards and the level of risk, work out how to fix them. If you can’t eliminate the hazard then decide what controls to put into place, use the ‘Hierarchy of Risk Control’ pyramid. List the controls that are needed to keep employees safe e.g. setting up an exclusion zone, using 3 points of contact when climbing onto the truck, using a spotter…..
- Now write your Safe Work/Operating Procedure, you can find a template here: https://www.worksafe.qld.gov.au/injury-prevention-safety/small-business/compliance-at-a-glance-serious-about-safe-business/safe-work-procedures I find it best to start with the PPE that is needed, then I break the task up into 3 parts.
- Pre-Operational Safety Checks – what to check and look for before you start the operation e.g. safety guards, damaged cords, clean and clear work area, exclusion zones
- Operational Safety Procedures – how to perform the task safely e.g. keep hands and feet inside the carriage at all times, do not lick wet paint…
- Housekeeping – After you complete the task e.g. turn off and unplug from the wall, refuel equipment….
- Train your staff to ensure they understand the hazards and the control measures they must always follow, have them sign the SOP and update your training record
- Supervise your staff to ensure they are competent in completing the task. Retrain if necessary and if conditions are different to when staff were trained check that your staff are competent in the different conditions
- Review your procedure to ensure it is correct, update when changes or an incident occurs
Projects One Safety Online has a small library of Safe Operating Procedures for our clients to use. Save time and money with Projects One Safety Online
Get started with Projects One Safety Online to take care of your daily safety paperwork needs. Save time, complete your Risk Assessments, SWMS, and Toolbox meetings online on your phone onsite
Projects One Safety Online keeps track of your projects, gives your staff the information they need for that task, allows your staff to add notes and keep a complete file for all members of the project to see
Remember, every morning as you prepare for work ask yourself, what’s different about today? If something is different you need to revise your safety!